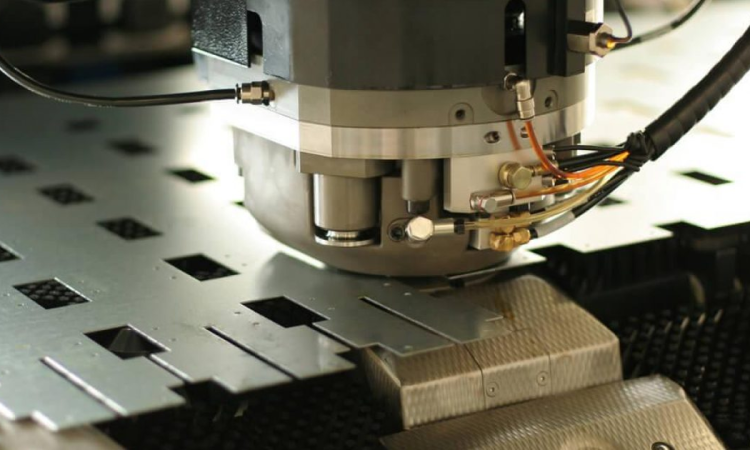
In the world of manufacturing, producing large quantities of metal parts efficiently, precisely, and cost-effectively is a top priority for many industries. From automotive to aerospace, electronics to appliances, the demand for high-quality metal components continues to grow. Among various manufacturing processes, conventional metal stamping stands out as an optimal choice for meeting large-scale metal part requirements. This article explores the reasons why conventional metal stamping remains the best option for businesses seeking reliability, consistency, and scalability in metal part production.
Understanding Conventional Metal Stamping
Conventional metal stamping is a manufacturing process that involves placing flat sheet metal into a stamping press where a tool and die surface form the metal into a desired shape. The process can include a variety of techniques such as punching, blanking, embossing, bending, and coining. Unlike some modern, more specialized methods, Conventional Metal Stamping relies on well-established mechanical presses and durable dies, making it highly versatile and suitable for a broad range of metals and part geometries.
This method is widely favored because it can handle high production volumes while maintaining tight tolerances and excellent repeatability. It is especially effective for manufacturing parts that require intricate designs or consistent features across thousands or millions of units.
High Efficiency for Mass Production
One of the strongest advantages of conventional metal stamping is its efficiency in large-scale manufacturing. The process is designed for speed and volume, enabling manufacturers to produce thousands of parts per hour once the initial setup is complete. The upfront investment in tooling and die creation may be considerable, but it quickly pays off through rapid, continuous production runs.
For industries that require large batches of identical metal parts—such as automotive body components, electrical housings, or industrial fasteners—conventional metal stamping offers unmatched productivity. Automated feeding systems and multi-stage presses further enhance throughput, making it possible to achieve tight delivery schedules without sacrificing quality.
Precision and Consistency
When producing metal parts at scale, precision is paramount. Conventional metal stamping provides consistent dimensional accuracy and repeatability, ensuring that each component meets exact specifications. This level of precision is critical for applications where tight tolerances affect the performance and safety of the final product.
Because the process uses hardened steel dies that shape the metal in a controlled manner, the resulting parts have uniform thickness, smooth edges, and defined features. The high consistency reduces the need for secondary finishing operations and minimizes scrap rates, which in turn lowers overall production costs.
Cost-Effectiveness Over Time
While the initial tooling investment for conventional metal stamping can be high, the long-term cost benefits are significant. The durability of stamping dies means they can withstand millions of cycles, allowing manufacturers to amortize tooling costs over a large number of parts. This advantage is especially pronounced for companies producing large volumes of the same part or components with similar designs.
Moreover, the speed of production reduces labor costs, and the efficiency of material usage in stamping processes minimizes waste. These factors combine to make conventional metal stamping one of the most economical manufacturing methods for high-volume metal part production.
Versatility and Material Compatibility
Another reason conventional metal stamping is a preferred option is its ability to work with a wide variety of metals, including aluminum, brass, copper, stainless steel, and carbon steel. This flexibility allows manufacturers to choose the optimal material based on the application’s mechanical, electrical, or corrosion resistance requirements.
Additionally, conventional stamping can produce complex shapes that would be difficult or expensive to create using alternative methods. From simple flat parts to three-dimensional components with intricate bends and cutouts, conventional metal stamping adapts well to diverse design needs.
Scalability and Adaptability
For businesses anticipating growth or fluctuating demand, conventional metal stamping offers excellent scalability. Once the tooling is designed and tested, increasing production volumes requires relatively little additional setup, allowing companies to ramp up output quickly to meet market needs.
Furthermore, if product designs evolve, existing dies can often be modified or replaced with minimal disruption. This adaptability makes conventional metal stamping a future-proof choice for manufacturers who require both high output and flexibility.
Conclusion
In conclusion, conventional metal stamping remains the best solution for large-scale metal part production due to its efficiency, precision, cost-effectiveness, versatility, and scalability. Its proven ability to deliver high-quality components at volume makes it indispensable across numerous industries that rely on metal parts for their products. When selecting a manufacturing process to meet large-scale metal part needs, conventional metal stamping stands out as the most reliable and economically sound option, ensuring manufacturers can maintain competitive advantage while meeting demanding production schedules.